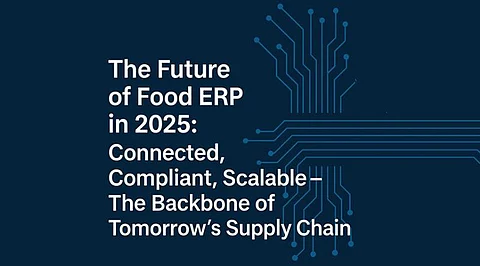
In 2025, food manufacturers, distributors, and processors find themselves at a crossroads. As supply chains become more fragile and consumer expectations tighten around freshness and safety, traditional systems are no longer enough to keep operations running smoothly. The risks of expired inventory, weak lot traceability, and ineffective stock control are no longer occasional hiccups—they're recurring problems that eat into margins and erode customer trust.
This is where the evolution of food ERP software becomes more than a digital tool—it becomes the nerve center of the modern food supply chain. A well-built ERP doesn’t just keep records. It enforces discipline, keeps products moving in the right order, and ensures that every stakeholder—from the warehouse picker to the CFO—has a clear view of the business.
Let’s explore how food ERP is changing in 2025 and what this means for businesses trying to stay fresh, safe, and profitable.
Many food businesses still rely on a mixture of spreadsheets, manual logs, and outdated software. These patchwork systems may have gotten the job done in the past, but they’re showing cracks under today’s pressure. Problems like expired stock, missing lot numbers, and poor visibility across locations are symptoms of deeper issues: disconnected data and delayed decisions.
In contrast, modern Food ERP software unify operations. They connect purchasing, inventory, production, quality control, sales, and compliance into a single, real-time platform. This means fewer blind spots, faster decisions, and fewer costly surprises. When every part of the supply chain speaks the same language, the entire business becomes more responsive and resilient.
For many food producers, inventory management still revolves around spreadsheets, aging software, and gut instinct. While this may have worked in the past, the margin for error has shrunk. Today, a mismanaged batch can trigger expensive recalls, lost contracts, and compliance fines.
The challenge isn't just about being “digitally behind.” It's about falling short in three critical areas:
Inventory turnover slows when old stock lingers too long on the shelf.
Expired products quietly pile up in storage, draining profitability.
Traceability gaps surface when it's too late—during audits, recalls, or customer complaints.
The future of food ERP isn't just about replacing outdated systems. It’s about building a new kind of visibility—one where data isn’t buried, and decisions aren’t delayed.
FEFO—First Expired, First Out—has quietly become the standard in responsible food operations. While FIFO (First In, First Out) works in some sectors, it doesn't guarantee freshness in categories like dairy, bakery, and ready-to-eat meals.
Modern food ERP inventory control systems make FEFO practical. Instead of relying on manual checks, these systems assign expiry dates at the lot level and prioritize movement accordingly. That means no more guesswork at dispatch time. The system knows which batch needs to leave first and enforces that decision across locations and departments.
With Folio3’s FoodTech ERP, food businesses can operationalize FEFO with precision. It's built-in inventory logic automatically routes products based on expiry, helping businesses minimize waste while protecting quality
Lot traceability used to be a nice-to-have for audits or certifications. In 2025, it’s a frontline defense against both safety failures and supply chain disruptions.
A connected ERP system records lot numbers at every stage: when raw material enters the warehouse, during production, and when it ships out. If something goes wrong—a contamination report, an allergen mix-up, or a regulatory red flag—you can trace it back to the source within minutes.
But traceability isn’t just about responding to problems. It’s about preventing them.
If a supplier batch is recalled, you know which products used it.
If a customer reports an issue, you don’t have to shut down entire lines—you isolate the affected lot.
If compliance officers come knocking, your records speak for themselves.
This isn’t just better tracking. It’s smarter risk management, powered by a food ERP designed with traceability as a core principle. That’s the kind of confidence Folio3 FoodTech ERP brings to the table. With its lot-level tracking and recall management tools, your traceability strategy becomes proactive rather than reactive.
Food businesses don’t make money by stockpiling—they earn by moving product. Slow turnover isn't just an operational issue—it’s a financial red flag. The longer items sit, the greater the chance they expire, get damaged, or tie up cash that could be used elsewhere.
In 2025, food ERP systems function as inventory coaches. They highlight slow movers, flag aging stock, and suggest purchase order quantities based on real trends, not outdated forecasts or intuition.
By connecting procurement, production, and sales data, modern food ERP software:
Prevents overproduction
Reduces emergency purchases
Keeps expiry risk front and center
Inventory turnover is no longer a passive metric. It’s actively managed with insights drawn from live data. Folio3’s FoodTech ERP empowers food businesses to optimize turnover with dynamic dashboards and AI-driven forecasts. This helps teams manage procurement and production with agility, keeping inventory lean and sales-driven.
Multi-location food businesses face a unique challenge: What’s available in one facility may not be usable in another. And when you're supplying to retail chains, restaurants, and direct-to-consumer channels simultaneously, errors multiply.
In 2025, food ERP inventory control must cover:
Bin-level visibility: Not just what’s in stock, but where exactly it sits.
Channel-specific allocation: Ensuring the right product goes to the right buyer.
Expiry-aware transfers: Moving inventory without passing along near-expiry items.
Whether you're a fresh produce supplier or a packaged goods processor, centralizing this data in one ERP system is the only way to avoid overpromising and underdelivering.
Regulations in food manufacturing are evolving faster than ever. From FSMA and HACCP to global export requirements, compliance now cuts across departments—from purchasing to shipping.
In 2025, food ERP software will carry this burden quietly but effectively. They:
Validate supplier certificates before goods are received
Enforce allergen separation during batch processing
Track temperature logs from cold storage units
Store audit-ready records with timestamps and digital signatures
This isn’t about ticking boxes. It’s about making compliance a by-product of doing things right. Folio3’s Food ERP simplifies compliance with embedded checks at every stage. From raw material intake to final shipment, your data trail is clean, complete, and compliant.
Many food businesses start small and scale quickly, especially in high-demand categories like plant-based foods, snacks, and frozen meals. But with growth comes fragmentation. More SKUs, more sites, more vendors, more complexity.
ERP systems of the past struggled here. Either they were too rigid or too bloated. The next generation of food ERP is built for modular growth. You don’t need to activate everything at once. You expand only what your business truly needs.
In 2025, scalability means:
Adding new warehouses without starting from scratch
Onboarding co-packers or third-party manufacturers into the same data model
Expanding into international markets with built-in localization tools
Scalability in ERP isn’t about software size. It’s about staying coordinated as the business stretches in multiple directions.
ERP in 2025 is no longer limited to user entries and scheduled reports. It’s connected to the physical world. Sensors track cold chain breaches. Scales send weights directly to production records. QR codes scanned at goods receipt instantly populate batch details.
This tight loop between digital systems and physical processes means fewer blind spots—and fewer excuses.
For example:
A temperature spike in a freezer triggers a lot of hold before dispatch.
A mixing tank completes a batch and auto-updates the finished goods count.
A delivery truck scan confirms load integrity before it leaves the dock.
ERP no longer waits for people to input what’s happened. It captures events as they unfold.
Dashboards aren’t new. But the difference in 2025 is relevance. Generic reports are giving way to food-specific KPIs:
FEFO compliance rate
Batch yield variability
Supplier rejection trends
Stock-to-sale aging curves
Lot resolution time in traceability audits
This level of analysis doesn’t just help operations—it gives finance and leadership teams the clarity to act decisively. Whether it’s trimming SKUs, renegotiating supplier terms, or adjusting order minimums, these insights are business tools—not IT luxuries.
For food companies dragging their feet on upgrading to modern ERP systems, the risks are piling up. It’s no longer just about inefficiencies. The costs show up in lawsuits, lost contracts, and product recalls.
Every expired pallet that ships out eats into customer confidence.
Every missing lot number adds hours to traceability investigations.
Every disconnected warehouse slows down decision-making just when speed matters most.
ERP isn’t a “tech investment” anymore—it’s operational insurance. It’s the backbone that holds your business steady when supply chains shake.
Food ERP systems in 2025 are not just about efficiency or convenience. They are essential infrastructure for any food business that wants to maintain freshness, ensure compliance, and grow sustainably.
With connected systems, accurate data, and real-time decision-making, ERP becomes the backbone of tomorrow’s supply chain. If your business is still struggling with expired stock, poor inventory turnover, or gaps in traceability, the time to act is now.
A modern Food ERP system doesn’t just support your business. It protects it. Folio3 FoodTech ERP is purpose-built to help food businesses solve these challenges head-on. It is more than software it is operational insurance for a complex and demanding industry.