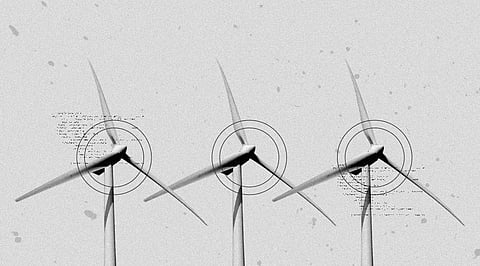
Wind turbine towers can create clean electricity but they frequently leak oil, damaging the blades, increasing wind resistance, and can even pollute the ground. The remote-controlled robots can minimize downtime on the wind turbines by cleaning and inspecting them without the intervention of human workforce.
Wind turbine inspection entails inspecting the key components that allow a turbine to function and produce energy. For this purpose, they use wind turbine inspection robots that are robotic devices that are used by onshore and offshore wind turbine operators for inspection of monitoring, and mitigating wear and tear on the parts. Over the course of the turbine's lifetime, less and less energy is produced as a result of erosion on the blades, as a result, regular wind turbine blade maintenance and inspection are crucial to maintaining the blades' structural integrity and extending the machines' life.
The wind turbine inspection and repair by the wind turbine operators are mainly on the blade. The erosion on the blades is a huge problem. The surface of the blade ages gradually which harms the blade's aerodynamics by wearing off the outer layer of the blade. Over time, less and less energy is produced as a result. The robotic wind turbine care system, Aerones, shows that robots can save downtime on wind turbines and can increase annual energy production by 12 percent. Turbine downtime rises due to larger turbines which cost more money as power prices rise. The Robots, used for maintenance and inspection, clean the towers and blades by spraying liquid detergent. They also collect contaminated liquid from skits and belts and funnel it to a filtering station. The Robots repair the blades by cleaning the damaged areas and filling any gaps or eroded surfaces using ultrasound scanning and cameras. The Robotic system is safe and cost-effective in checking for blade damage. This aspect is a significant driver for the adoption of wind turbine inspection and repair robots by the wind power industry. The method can be costly and failure of safety implications are considered in the case of downtimes and repairs caused by failure of both onshore and offshore renewable energy assets. As the wind blades are exposed to harsh climatic conditions, it often needs to be inspected on location. However, manual inspection is dangerous for operators using rope or aerial lift access which requires suitable conditions and is expensive for operators but the use of robots cuts down on potential hazards encountered with this. The designers of inspection robots also face challenges leading to a range of designs from those that use a combination of suction and tank tracks to traverse the surface of a blade, to suction-cup-legged inspect and repair robots.
A UK company released a wind turbine inspection robot 'BladeBUG' that inspects the task in 35 minutes, half the manual work time. It provides a fast, safe, and cost-effective alternative to rope access technicians inspecting blades. The robot is attached at ground level to a rope lowered by a technician from the top of the turbine, then hoisted into place to inspect the blade. One end of the rope is attached to a power descender on the ground, then goes up to the top to a pulley and back down to the robot. A top-down approach to deployment works best for offshore turbines. Because the BladeBUG does not need to be hauled to the top of the turbine, valuable time is saved when carrying out necessary onshore inspections. The founder of BladeBUG, Chris Cieslak explained: "The demonstration proved the EchoBoltBUG is not only capable of performing a bolt check for any loss of tension, but doing it in a much more autonomous way. The idea of the robot independently checking a set of bolts, without assistance, is now a reality and takes maintenance of wind turbines to the next level by making them safer and more cost-effective for operators."
The Latvian Robotics group Aerones has serviced more than 3,00 Turbines in 17 countries. The scale-up of wind energy is expected to double by 2030 with renewable energy sources becoming increasingly popular among investors which are offering a significant market opportunity for industries. The company is working on new robotics solutions for its pipelines which is a new model that inspects the inside of the turbines by crawling inside and scanning turbine blades, creating a digital twin of the information gathered, and a cleaning robot that removes oil and dirt from turbine towers.
Join our WhatsApp Channel to get the latest news, exclusives and videos on WhatsApp
_____________
Disclaimer: Analytics Insight does not provide financial advice or guidance. Also note that the cryptocurrencies mentioned/listed on the website could potentially be scams, i.e. designed to induce you to invest financial resources that may be lost forever and not be recoverable once investments are made. You are responsible for conducting your own research (DYOR) before making any investments. Read more here.