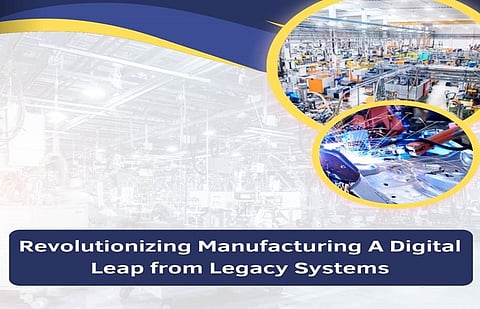
In the modern digital transformation era, manufacturing industries worldwide are undergoing a paradigm shift as they transition from outdated legacy systems to advanced digital platforms. Rajkumar Chindanuru, a prominent researcher, delves into the intricacies of modernizing manufacturing technology to enhance efficiency and scalability. His insights shed light on how digital transformation is shaping the future of industrial operations.
Legacy systems in manufacturing have become a significant barrier to efficiency and innovation. Outdated production tracking and payroll processing systems struggle to integrate with modern technologies, leading to rising maintenance costs, inefficiencies, and an increased risk of failures. Many enterprises continue to rely on aging infrastructure, limiting their ability to adapt to evolving market demands. These outdated frameworks hinder seamless connectivity with advanced solutions, restricting automation, real-time data access, and operational agility. As technology evolves, manufacturers must modernize their systems to remain competitive, enhance productivity, and reduce the long-term costs associated with legacy system maintenance.
A clearly outlined modernization strategy is the answer to all these shortcomings. One of the most effective methods is API-led integration, which connects older systems to newer systems.
This structured approach comprises cloud migration and microservices-based architectures to improve agility, increasing users' capabilities on the shop floor or in the field. The result is a continuous flow of information between enterprise applications such as customer relationship management and enterprise resource planning, minimizing integration time and improving interoperability.
It is impossible to have greater benefits that migrating from on-premises infrastructure to a cloud-based platform. This is because cloud solutions reduce the cost of hardware refresh and improve their availability and security. It is observed that manufacturers using cloud-native applications tend to gain maximum flexibility in their production with the passing of time and resists operational resilience with that phenomenon. This encourages organizations to use resources economically by scaling their resources without over-provisioning, therefore managing costs well.
An immediate production-tackling system has been established to track the efficiency of manufacturing. The manufacturers will be able to monitor their production against smart terminals and RFID scanners. The result here would be close to throwing away all material waste and reducing the effort required for redoing the work.
Manual errors with automatic data entry are eliminated, accuracy increased, and tax freed valuable human resources to do more strategic tasks. With modern payroll and automated processing, too, several benefits like increased efficiency and reduction of errors, faster processing times, and data security are offered that lead to reduced costs and improved compliance.
With the accelerating pace of digital transformation, cybersecurity must become more robust. Encrypting information at all levels and enforcing multi-factor authentication and strict access controls can prevent data breach and unauthorized access. Strom strengthening security protocols will not only protect confidential information but also keep the organization in compliance with industry regulations. Integration of regulatory norms with security measures will minimize the audit preparation cost and legal exposure. Proactive cybersecurity approaches, how all-round monitoring coupled with threat intelligence, further enhance resilience to the changing face of cyber threats. A rounded security architecture inspires confidence, protects critical assets, and allows seamless business operations within increasingly digital enclaves.
Advanced analytics will transform the manufacturing activities from data-driven decision-making into real-time operational action. They will use techniques such as predictive analytics to gain insight into their patterns in production data and proactively seek to remedy bottlenecks while optimizing resources and improving on-time delivery. Data warehouses that can create a more unified picture for a company by using all its internal data sources create the best environment for data-driven decision-making. This analytical approach enhances efficiency, reduces downtime, and fosters continuous process improvements. Manufacturers that embrace data-driven insights can respond swiftly to market demands, enhance productivity, and maintain a competitive edge in an increasingly complex and fast-paced industrial landscape.
A phased implementation strategy is crucial for a seamless digital transformation, minimizing disruptions and ensuring business continuity. By deploying new technologies incrementally, organizations can adapt gradually without operational downtime. Running legacy and modern systems in parallel during migration provides a safety net, enabling thorough validation of new capabilities before full transition. This approach mitigates risks, allows for real-time troubleshooting, and ensures a smoother shift to advanced infrastructure. A well-structured rollout plan fosters user adoption, reduces resistance to change, and enhances overall efficiency. Strategic planning and iterative execution are essential for a successful transformation with minimal business impact.
The adoption of cloud-native, API-driven architectures positions manufacturers for continued growth and technological adaptability. Standardized integration frameworks simplify the adoption of emerging technologies such as AI-driven quality inspection and IoT-based predictive maintenance. With a structured approach to modernization, businesses can enhance efficiency, reduce costs, and stay competitive in an increasingly digital marketplace.
In conclusion, Rajkumar Chindanuru’s research highlights the critical role of legacy system modernization in manufacturing. By adopting cloud computing, automation, and advanced analytics, manufacturers can enhance operational efficiency while achieving greater scalability and security. This digital transformation not only optimizes production workflows but also future-proofs businesses, positioning them for sustained success in an increasingly competitive industrial landscape.