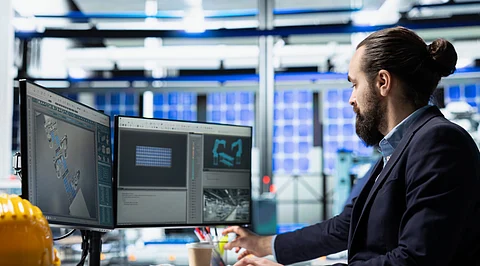
The manufacturing landscape has undergone a dramatic transformation over the past three decades. What once required hours of manual programming and guesswork now takes minutes with precision-driven automation. Computer-Aided Manufacturing (CAM) programs have become the cornerstone of this revolution, fundamentally changing how we approach production processes.
Think about it – just twenty years ago, programming a CNC machine meant manually writing G-code line by line. Today? A skilled operator can generate complex toolpaths in minutes, simulate the entire process virtually, and optimize for efficiency before the first chip ever flies. This isn't just an upgrade; it's a complete paradigm shift.
Back in the day, manufacturing relied heavily on:
Manual G-code programming – often taking 4-8 hours per part
Trial-and-error approaches on expensive machines
Extensive setup time and frequent tooling adjustments
High scrap rates due to programming mistakes
Machinists spend more time fixing programs than actually making parts.
Modern CAM systems have flipped this equation entirely. Here's what's changed:
The shift isn't just about speed – it's about intelligence. Today's CAM programs analyze material properties, tool characteristics, and machine capabilities simultaneously to generate optimal cutting strategies.
The numbers speak for themselves:
65-80% reduction in programming time
40-50% faster setup procedures
30-45% improvement in overall cycle times
But here's what really matters – this time saving translates directly to increased capacity without additional equipment investment.
Modern CAM systems deliver:
Micron-level accuracy in toolpath generation
Consistent quality across production runs
Reduced tool wear through optimized cutting parameters
Real-world impact: A medical device manufacturer reduced their rejection rate from 2.3% to 0.4% after implementing advanced CAM software – saving $180,000 annually in materials and rework costs.
CAM programs excel at:
Intelligent material usage – minimizing waste
Tool life optimization – extending cutting tool longevity by 40-60%
Energy efficiency – reducing power consumption through optimized feeds and speeds
The automotive sector has embraced CAM technology like no other. Take BMW's Spartanburg plant – they've achieved:
90% reduction in programming time for complex engine components
Zero-defect production runs of 10,000+ parts
50% faster time-to-market for new model tooling
In aerospace manufacturing, precision is non-negotiable. Companies like Lockheed Martin report:
99.7% first-time quality on critical components
60% reduction in manufacturing lead times
$2.3 million savings annually through optimized machining strategies
"CAM software has become our crystal ball – we can see exactly what will happen before we even touch the material," explains Sarah Chen, Senior Manufacturing Engineer at Northrop Grumman.
Medical device manufacturers face unique challenges with biocompatible materials and tight tolerances. CAM systems help by:
Generating ultra-smooth surface finishes critical for implants
Eliminating human error in complex geometries
Validating processes before expensive material commitment
Let's talk real numbers. A typical CAM implementation for a mid-sized manufacturer:
Initial Investment:
Software licenses: $25,000-$50,000
Training: $8,000-$15,000
Setup/integration: $10,000-$20,000
Annual Returns:
Labor savings: $120,000-$200,000
Material waste reduction: $35,000-$60,000
Increased throughput: $150,000-$300,000
Payback period: 3-6 months
But here's the kicker – these are just the direct savings. The indirect benefits often exceed the direct ones:
Faster response to customer demands
Ability to take on more complex projects
Reduced overtime and weekend work
Lower stress levels for programming staff
Modern CAM systems aren't just about generating toolpaths anymore. They're becoming intelligent manufacturing partners:
Real-time adjustment based on cutting conditions
Force monitoring to prevent tool breakage
Automatic parameter optimization for unknown materials
Seamless CAD integration – changes flow automatically
ERP system connectivity for production scheduling
Quality system integration for automatic documentation
Complete machine simulation including collisions
Material removal visualization
Cycle time prediction with 95%+ accuracy
For those just starting their CAM journey, understanding what is CAM software and its capabilities is crucial for making informed decisions about implementation.
The manufacturing revolution brought about by CAM is rarely on the horizon—it has already come into being. Those companies that choose not to accept that technology are facing a serious loss of competitive position.
The question isn't whether to implement CAM systems anymore, but rather how soon you can effectively implement them. These are your benefits: faster delivery times, better product quality, and a much better profit margin.
Bottom line: CAM has disturbed the serviceable manufacturing processes existing today. They have taken difficult, time-consuming processes and allowed them to be predictable and streamlined. In short, they are indispensable for a manufacturer wishing to stay competitive in the present-day market.
Are you ready to reinvent your manufacturing processes? This technology works; the benefits have been proven; now it's up to the trailblazers to forge a competing advantage in the new-age manufacturing.