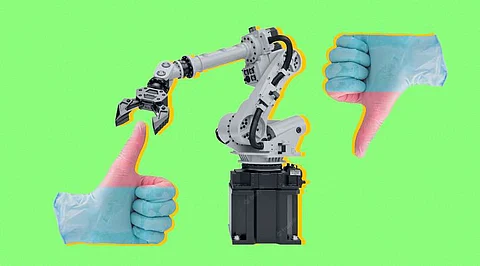
In the ever-evolving landscape of the manufacturing industry, the integration of automation has become a defining force, reshaping traditional paradigms and paving the way for unprecedented advancements. With the fusion of cutting-edge technologies such as robotics and artificial intelligence, the manufacturing sector stands at the cusp of a transformative journey. This article delves into the multifaceted realm of automation, unraveling its myriad benefits and potential drawbacks.
From enhancing operational efficiency to redefining workplace safety, the pros of automation offer a compelling vision of the future. However, it is equally crucial to navigate the challenges of initial investment, job displacement, and technical intricacies. By striking a harmonious balance between innovation and human expertise, the manufacturing industry can harness the power of automation while safeguarding its legacy and workforce.
One of the most compelling advantages of automation in manufacturing is the remarkable increase in efficiency and productivity. Automated systems can operate 24/7 without fatigue, significantly accelerating production cycles. With minimized human intervention, the risk of errors and inconsistencies is greatly reduced, ensuring higher product quality and fewer defects.
Automation can lead to substantial cost savings over the long term. While initial setup costs can be significant, the return on investment can be substantial due to reduced labor expenses, decreased scrap rates, and optimized resource utilization.
The implementation of automation in manufacturing can mitigate workplace hazards by transferring dangerous tasks to machines. This not only safeguards the well-being of employees but also reduces the likelihood of accidents and injuries. Workers can focus on overseeing and maintaining automated systems, creating a safer and more conducive work environment.
Automation ensures a consistent level of product quality and precision that is challenging to achieve through manual processes. Complex tasks can be executed with a high degree of accuracy, leading to standardized products that meet or exceed customer expectations. This consistency can enhance a company's reputation and customer satisfaction.
Automation brings with it the advantage of generating vast amounts of data related to various aspects of the manufacturing process. This data can be collected, analyzed, and used to make informed decisions that optimize production efficiency and resource allocation. Manufacturers can gain valuable insights into production trends, equipment performance, and product quality, allowing them to make proactive adjustments and improvements.
The upfront costs associated with implementing automation can be substantial. Acquiring and integrating automated systems, machinery, and software require a significant financial investment. Small and medium-sized enterprises (SMEs) may find it challenging to bear these initial expenses, potentially limiting their ability to compete on the same scale as larger corporations.
As automation takes over repetitive tasks, the demand for certain manual jobs may decrease, leading to job displacement for some workers. This can result in economic and social challenges, requiring retraining and upskilling programs to ensure a skilled workforce for new roles that emerge alongside automated technologies.
The rapidly evolving nature of technology presents a challenge for manufacturers looking to keep up with the latest advancements. Implementing and maintaining automated systems require specialized technical expertise, and manufacturers must continuously invest in training and updates to remain competitive.
While automation offers numerous benefits, it also introduces the risk of technical failures. Malfunctions, system crashes, or software glitches can disrupt production processes and lead to downtime. To mitigate this risk, companies must invest in robust maintenance and backup systems, which can entail additional costs.
The implementation of automation often relies on consistent and reliable energy sources to power the automated systems and machinery. Any disruptions in power supply or infrastructure can lead to downtime and hamper production. Manufacturers must consider the potential impact of energy fluctuations or shortages on their operations and invest in backup power solutions or alternative energy sources to mitigate these risks.
Join our WhatsApp Channel to get the latest news, exclusives and videos on WhatsApp
_____________
Disclaimer: Analytics Insight does not provide financial advice or guidance on cryptocurrencies and stocks. Also note that the cryptocurrencies mentioned/listed on the website could potentially be scams, i.e. designed to induce you to invest financial resources that may be lost forever and not be recoverable once investments are made. This article is provided for informational purposes and does not constitute investment advice. You are responsible for conducting your own research (DYOR) before making any investments. Read more about the financial risks involved here.