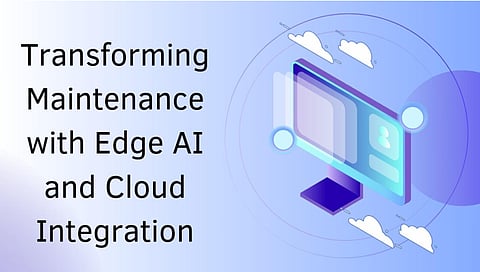
In the industrial world, predictive maintenance has emerged as a game-changer, driven by the strategic integration of edge computing, artificial intelligence (AI), and cloud infrastructure. Akhilesh Kota, a distinguished innovator in this field, explores the seamless fusion of these technologies to address the persistent challenges of unplanned downtime and equipment failures. His work not only highlights innovative solutions but also provides a roadmap for organizations aiming to enhance efficiency and reduce costs.
Traditional methods of maintenance have not been able to cope with the growing complexities of industrial equipment. Reactive maintenance is a "run-to-failure" basis that leads to much time spent on downtime. The unplanned breakdowns take up a whopping 72% of maintenance budgets. Preventive maintenance, though better organized, usually leads to unwarranted interventions that waste resources and drive costs higher. These traditional methods are ill-suited for the high-speed production setting, where minor machinery failures can shut down the production and lead to millions of dollars in losses. As industries change, the requirement for a more intelligent and proactive method to eliminate inefficiencies, costs, and risks has become the need of the hour. Advanced, data-driven maintenance systems are now a necessity in order to deal with the rising issues in the industrial setup.
Edge computing represents a transformational move for industrial maintenance, making real-time data analysis at the source machine possible. Edge devices reduce system latency from tens of hundreds of milliseconds down to 16 milliseconds by locally processing vast amounts of sensor data. This does not only make efficiency operational but also conserves bandwidth usage, significantly cutting costs linked to cloud computing by 76%. Modern edge systems are geared to process input streams from more than one sensor, transforming the raw data to meaningful insights. They can, for instance, find anomalies in the equipment up to 36 hours before traditional ways do, enabling the prevention of costly downtime. Edge systems are also remarkably resilient, maintaining autonomous operation without networks, keeping on analyzing without fail and steadily performing for very long periods of time.
The strength of edge computing is being able to compute at the point where data resides, thus producing real-time insight and rapid decisions. However, if combined with cloud computing, it opens further opportunities for tremendous storage of large data, detailed analysis of histories, and a model of big predictions. Thus, cloud computing enables complex analytics and informed decision-making across the operations, supporting complex analytics over the operations where 147 terabytes of sensor data may be processed by the facility yearly. Hybrid edge-cloud architectures also reduce data processing latency by 84% compared to traditional systems. In addition, through the power of advanced machine learning, cloud systems fine-tune predictive algorithms that achieve an incredible 93.7% accuracy in detecting possible equipment failures, making industrial operations smarter and more reliable than ever before.
In synergy, edge and cloud computing bring a significant breakthrough to predictive maintenance, combining the strengths of both. Edge devices are very good for real-time data analysis and take care of immediate, time-sensitive tasks, whereas cloud platforms provide a more comprehensive perspective in terms of cross-facility benchmarking and long-term strategy optimization. This combination has translated into measurable benefits from improvements such as reduction in maintenance costs by 28.5% and improving predictions of the lifespan of equipment by 41%. In addition, such systems offer unmatched scalability and security due to the utilization of sophisticated encryption protocols as well as intelligent recovery mechanisms for increased resilience and reliability, even under the toughest industrial conditions, towards smarter and more efficient operations.
The future of predictive maintenance lies in the hands of advanced AI, sophisticated sensors, and better connectivity. Transfer learning and federated AI are the kind of technologies that promise to change the game in terms of reducing the time it takes to train models, and enhancing the accuracy of predictions. Cutting-edge sensors have made data collection unprecedentedly deeper for equipment performance and health. Explainable AI frameworks are becoming an essential requirement as well, creating trust and transparency in AI-driven decisions. All of these innovations can ensure up to 78% less downtime and extend the equipment lifespan by almost 30%. That will raise new standards in industrial efficiency and reliability.
In conclusion, Akhilesh Kota’s work highlights a transformative fusion of edge and cloud technologies, addressing inefficiencies in traditional maintenance systems. By leveraging advanced AI and innovative solutions, he envisions a future where industrial operations are smarter, safer, and more efficient. As organizations embrace these advancements, predictive maintenance will continue to drive operational excellence, reducing downtime and enhancing equipment reliability, ultimately setting a new standard for industrial efficiency and innovation.