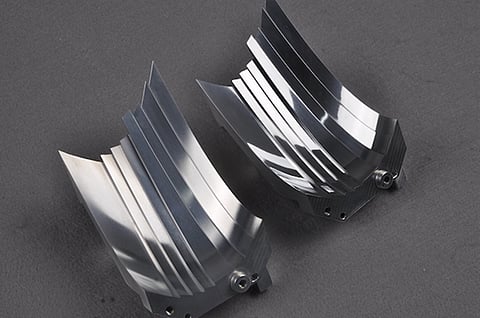
With the rapid development of science and technology, AI has gradually penetrated into various fields, including CNC machining. CNC machining services is the core part of modern manufacturing, and its efficiency and accuracy directly affect the quality of products and production costs. The application of AI has brought revolutionary changes to CNC machining, which can greatly improve the efficiency and accuracy of machining.
(1) Accuracy Improvement: AI can control and optimize the CNC machining process more accurately through deep learning and big data analysis. For example, AI is able to accurately predict tool wear through real-time monitoring of vibration, temperature, sound and other small changes in the cutting process, so that real-time adjustments can be made during the machining process to ensure machining accuracy.
(2) Efficiency optimization: AI can quickly analyse a large amount of machining data to find the optimal combination of machining parameters, such as cutting speed, feed rate and depth. This optimization not only improves machining efficiency, but also reduces tool wear, extends tool life and reduces production costs.
(3) Increased automation: AI can fully automate CNC machining tasks, automatic programming, from tool path planning, cutting process control, to quality inspection. And no manual intervention is required, which can save a lot of time and effort and make the production line more efficient. This kind of automation can reduce the requirements for workers' skills, reduce the chance of human error and improve production stability.
(4) Responding to complex tasks: for some complex and delicate parts processing, AI can ensure the accuracy and consistency of the processing process through high-precision modelling and simulation.
(5) Failure warning: AI can monitor the operating status of the machine tool in real time and predict possible failures in advance by analysing various sensor data. In this way, maintenance personnel can intervene before the failure occurs, reducing downtime and improving equipment utilisation.
(6) Strong flexibility: AI has a strong learning ability and adaptability, and can quickly adapt to different processing environments and conditions. When processing needs change, AI can quickly adapt to the new production environment by re-learning and adjusting.
(7) Data-driven decision-making: AI can transform a large amount of production data into valuable information to provide managers with a basis for decision-making. For example, through the analysis of historical machining data, key factors affecting machining efficiency and accuracy can be identified to further optimize the production process.
1. Intelligent identification and positioning
In CNC machining, an accurate positioning method can ensure the accuracy and stability of machining. Through AI technology, intelligent identification and positioning of the workpiece can be achieved.
First, a large number of pictures and samples containing the target workpiece are collected, and even images containing different scenes. For example, images at different angles or under different lighting conditions;
The collected images are then processed to extract features, such as edges and shapes;
The extracted features and corresponding labels are then used to train the AI model so that the model is able to recognise the type of workpiece based on the input information.
Afterwards, the optimised model can be deployed into the actual production environment by adjusting the model parameters so that the machine can automatically identify the features of the workpiece and determine its position and attitude. It even quickly and accurately identifies information about the processed material, including the type, size and material of the material.
This information is crucial to the subsequent processing, helping to ensure the accuracy and efficiency of processing, so as to achieve rapid and accurate positioning of the workpiece.
2.Intelligent programming
Through AI technology, machining programs can be automatically identified and generated to reduce the time and error of manual programming; cutting parameters, machining paths, etc. can be automatically optimised according to the processing requirements to improve processing efficiency. Using machine learning algorithms, the language and rules of CNC programming are trained and a model is generated so that it can automatically generate executable CNC programs.This can significantly enhance the efficiency in the early development stages and achieve more accurate realization of the prototype concept.
This model can generate CNC programs by engaging in a dialogue with a human and generating the appropriate instructions as required. Only verbal instructions need to be entered instead of having to manually write complex CNC programs, which makes the programming process easier and more efficient while avoiding the errors associated with manually writing CNC programs, improving machining accuracy and quality, and reducing waste.
In conclusion, the application of AI in CNC machining has achieved remarkable results, which can effectively improve machining efficiency, precision and equipment reliability, and promote the transformation and upgrading of the manufacturing industry, but it is also a double-edged sword, and it is necessary to pay attention to and solve the problems and challenges that may be brought about while enjoying the convenience it brings.