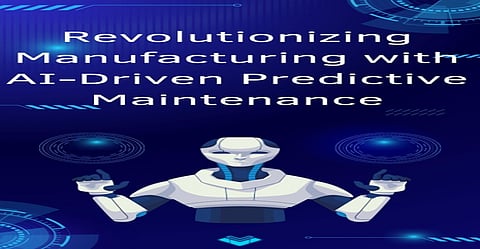
The manufacturing industry rapidly integrates automation and AI-driven cloud storage, especially predictive maintenance. These technologies help reduce unplanned downtime, optimize efficiency, and raise productivity. Against this backdrop, Vamsi Krishna Rao explores in this article the innovative impact on the transformation of the manufacturing practice.
IoT sensor devices across the production lines monitor key parameters like vibration, temperature, and pressure and provide real-time data for sound and timely decisions. MEMS-based accelerometers and piezoelectric sensors offer high-resolution data on the functioning of equipment and conditions prevailing in the environment. AI algorithms interpret this data for predictive insights, while large data volumes are managed by cloud platforms such as AWS IoT Core and Microsoft Azure IoT Hub. These solutions consolidate storage and allow for data that is always accessible across locations to the manufacturers with critical, real-time information.
AI is revolutionizing the conventional strategies of maintenance by means of machine learning and deep learning algorithms. Predictive maintenance systems can now identify anomalies and predict equipment failures long before it happens through historical data and new information in models. The use of anomaly detection, time series analysis, and CNNs for image-based fault detection is a method of monitoring the health of equipment. AI-driven approaches help maintenance teams take proactive actions by detecting subtle patterns and preventing potential failures before they become significant issues.
AI-driven predictive maintenance is good at continuous monitoring of equipment performance and analyzing sensor data in real time. These systems incorporate advanced signal processing as well as advanced pattern recognition algorithms that can even sense very minute variations in behavior just to give warnings for interventions prior to the point of occurrence. A direct benefit is the mechanization of scheduled maintenance. The AI platform will consider factors such as time to failure prediction, manufacturing schedules, and resources available in generating optimized schedules that ensure maintenance occurs at the best time while minimizing production disruption during improvement of equipment reliability.
Predictive maintenance, with AI technologies, decreases expenses and improves the lifespan of equipment by detecting problems earlier and optimizing the time for repair, thereby increasing the age of equipment by 25%. AI-based systems reduce the cost of maintenance by up to 15-20% with minimum interventions and optimized utilization of resources. Improved utilization of equipment and reduced delays save both money and time and add value.
The AI-driven predictive maintenance system, with its cloud-based nature, ensures real-time data access across departments and locations. This enhances coordination between production and maintenance teams, enabling remote diagnostics and faster decision-making. Cloud integration also allows insights to be shared, promoting continuous improvement and creating a more agile, responsive manufacturing environment.
This has led to AI-driven predictive maintenance being adopted on a mass scale and speeding up the pace toward totally automated, self-monitoring production facilities. Within the Industry 4.0 paradigm, such systems are connected with other smart technologies, including autonomous robots and digital twins, in order to build a more comprehensive ecosystem of self-regulating production lines. It will not only be more operationally efficient but also reduce manual intervention, making room for smarter and more autonomous manufacturing processes.
The advantages of AI-based predictive maintenance systems are obvious, but some initial investment is known to be pretty expensive; it also integrates challengingly with legacy systems and requires many specific skills. Data security and privacy issues as well as workforce adaptation will remain as the critical challenges. Overcoming these hurdles is mandatory to ensure realization of the benefits across industries through AI-driven maintenance systems.
The future of AI-driven predictive maintenance is quite promising with new technologies such as digital twins and 5G that will further improve the accuracy and capabilities of predictive maintenance. Beyond manufacturing, the potential of AI is being harnessed across industries such as energy, transportation, and healthcare. This evolution, therefore, represents an ongoing series of opportunities for innovation, thus making AI-driven predictive maintenance an integral part of the Industry 4.0 revolution.
In a nutshell, Vamsi Krishna Rao says that AI-based cloud storage systems are bringing a change in predictive maintenance in manufacturing by saving time on unnecessary downtime, extended life cycle for equipment, and thus colossal cost-effectiveness. With every technological upgradation, there will remain the overall effect on increased operational efficiency along with industry-changing impact, which will lead to completely automated environments of production as well as self-surveillance.